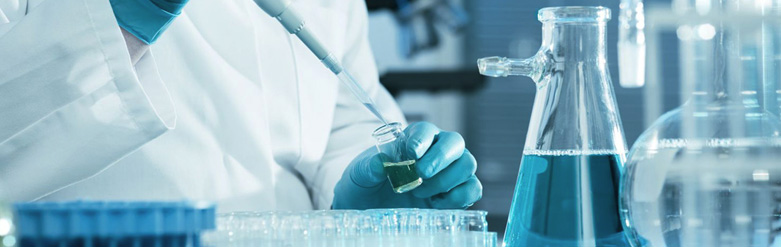
Expertise in thermodynamics as well as chemical, mechanical, and biomedical engineering allows our engineers to create innovative temperature controlled packaging solutions that are shipped to manufacturing fill and finish locations, hospitals, clinics, specialty pharmacies, and retail pharmacies worldwide.
As an engineering focused organization, our team uses advanced computer aided engineering and thermal modeling to design and validate products which are then qualified and pre-certified in our two ISTA certified labs. Our three walk-in chambers and two reach-in thermal chambers can simulate temperatures from -30 to 70 C. Close interaction between labs and manufacturing enables rapid time to market and stability of supply from one of our many facilities worldwide.
Innovation and Development Process
Our innovation process starts with a robust understanding of customer needs and the demands placed on the product from manufacture through patient use.
Select an icon below to learn about our capabilities in each area :
Concept and Design
In this phase, customer cold chain packaging needs are identified. Things like mass criteria, temperature requirements, shipment type, length of transit/storage, etc. are documented, specifications are created and concepts generated. The concepts start with mechanical drawings of configurations, gel packs, and load capabilities. These drawings help define initial costs, size and performance.
Simulation Testing
By building several configurations in a simulated environment, our engineers can then test for hot spots and adjust designs. We can also create and test materials that do not currently exist permitting us to truly design the right solution for your cold chain needs. Simulation testing allow us to test without physically building the solution and helps us determine the effects of optimizing weight, gel, and materials. Working closely with our customers during this phase is especially essential.
Thermal Modeling
As experts in thermal dynamics, our engineers are able to use the latest in thermal modeling techniques and technologies to expedite the development process. Thermal solutions are evaluated using computer aided engineering (CAE), including computation fluid dynamics (CFD) and finite element analysis (FEA). Our powerful thermal modeling programming yields high accuracy enabling our engineers to identify hot spots, reactions, and other visuals, all before spending money on tooling and expensive materials.
Rapid Prototyping
At this stage, molds are created, parts injected and tooling developed to create orderable samples. In-house CNC machines quickly cut out samples of EPS, PUR, and ePURâ„¢ coolers to exact specifications.
Testing and Validation
Testing and validation services include not only simulation testing, but also operation qualification testing. Parts are evaluated and qualified for both thermal and mechanical performance. As one of the few ISTA standard 20 certified labs, real-time testing will produce accurate Design Qualification / Operational Qualification (DQ/OQ) reports, and create all protocols and reports. Performance Qualification (PQ) is then conducted for drop, shock and vibration testing along with thermal verification.